Manufacturing Processes
Sanyo Special Steel offers “Steel You Can Count On”
produced by the special steel manufacturing equipments
which realize high-quality and stable supply.
We produced stably high-quality special steel by special steel manufacturing equipments having outstanding production capacity, including steelmaking plants realizing the world’s highest level of cleanliness, forging and rolling equipments meeting the diverse needs of customers, and seamless tubes manufacturing equipments.
Furthermore we encourages the improvement of operational techniques and equipment in order to save energy and reduce environmental loads, with the goal of securing the confidence of both the market and society.
- Scrap melting
- Refining
- Casting
- Billet rolling / inspection
- Rolling / forging
- Steel tube manufacturing
- Inspection
Scrap melting
Scraps are melted in an electric furnace. Molten steel is poured into a large pan called a “ladle.” Our electric furnace is designed so that molten steel is poured into the ladle through the bottom of the furnace, which prevents oxidized slag, generated in the furnace, from mixing with the molten steel.
-
Refining
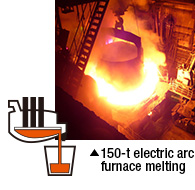
Refining
The ladle furnace removes impurities such as oxygen and sulfur from the molten steel in the ladle, and then alloying elements are added to adjust compositions. The molten steel is then circulated in the vacuum tank of the RH vacuum degasser to remove unnecessary gas components such as oxygen and hydrogen.
-
Casting
-
Scrap melting
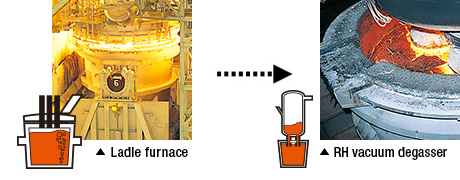
Casting
Refined and degassed molten steel is cast (solidified) in a continuous caster to create blooms.
-
Billet rolling / inspection
-
Refining
【 “Vertical-type” continuous caster that produces high-quality products 】
Continuous caster are classified roughly into the “vertical type” and the “curved type.” Blooms are solidified without being bent in the vertical-type machine, while blooms are bent horizontally before solidification in the curved type. The vertical-type machines require large-scale construction work, compared with the curved type, but they feature a number of advantages. A wide variety of steel types can be cast continuously and minor amounts of non-metallic inclusions remaining in the steel buoy up during casting, making it easy to remove them. Because of these reasons, Sanyo Special Steel has incorporated “vertical–type” continuous caster.
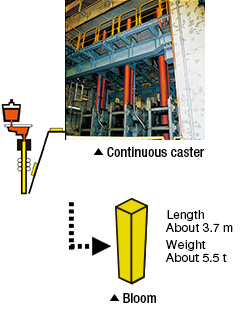
Billet rolling / inspection
Blooms cast in the continuous caster are rolled by a cogging mill or a billet rolling mill and processed into intermediate products called a billet. All of the billets undergo an intermediate inspection to check their quality.
-
Rolling / forging
-
Steel tube production
-
Casting
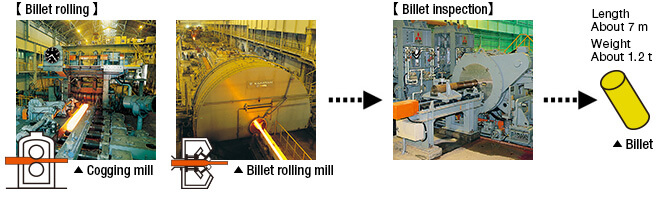
Rolling / forging
Billets produced at the bloom plant are rolled into steel bars of various sizes by machines such as a rolling mill.
-
Inspection
-
Billet rolling / inspection
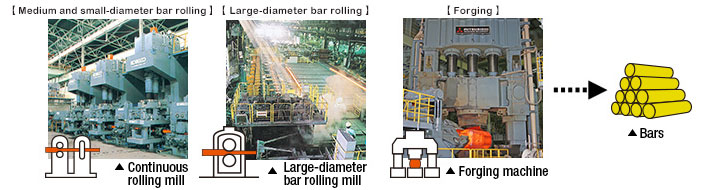
Steel tube manufacturing
Billets produced at the bloom plant are processed into tubes by an assel tube rolling mill or a hot extrusion press. The steel tubes are rolled further by a cold pilgering mill, if needed. Sanyo Special Steel is the only Japanese special steel manufacturer that has seamless steel tube manufacturing equipment.
-
Inspection
-
Billet rolling / inspection
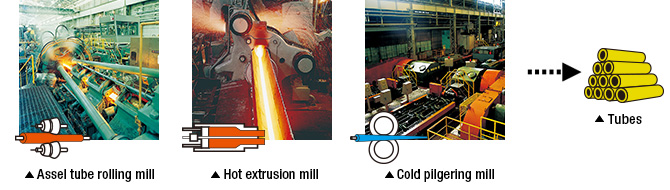
Inspection
All products undergo a bloom inspection to carefully check for surface flaws and the internal quality of billets, followed by a final inspection before delivery. Sanyo Special Steel has high-precision and effective non-destructive inspection machines including an automatic magnetic leakage flux inspection machine, an across-the-section ultrasonic inspection machine and a phased-array ultrasonic inspection machine – introduced into mass production for the first time in the world – to guarantee the quality and ensure a constant supply of special steel.
-
Rolling / forging
-
Steel tube production
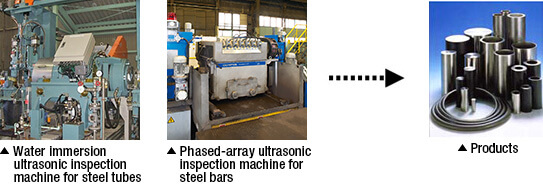
-
Special Steel Manufacturing Process(PDF:390KB)
-
Fabricated and Special Manufacturing Processes(PDF:1,283KB)
AcrobatReader is required to view PDF files.
Download